Aerospace manufacturers know all too well that even the smallest components can have massive consequences for an aircraft’s overall performance and safety.
Fasteners—bolts, screws, rivets—hold together critical structures that must withstand extreme stress, temperature fluctuations, and potentially corrosive conditions. A single faulty fastener, therefore, can compromise the integrity of an entire system.
Because of these high stakes, the aerospace industry relies on two important frameworks to ensure safe, consistent production: NADCAP (National Aerospace and Defense Contractors Accreditation Program) and AMS (Aerospace Material Specifications).
Which Standards Guide Aerospace Industry Manufacturing?
NADCAP represents an industry-led initiative that evaluates special processes such as heat treatment or nondestructive testing for aerospace components. Accredited facilities must maintain rigorous documentation and adhere to approved methods, demonstrating that their processes consistently meet stringent quality requirements.
Meanwhile, AMS provides the nuts-and-bolts specifications for materials and their heat-treat processes. In the case of fasteners, AMS lays out strict temperature ranges, recommended soak times, and target mechanical properties (like hardness) that must be achieved.
Passing NADCAP audits and conforming to AMS ensures a manufacturer’s production line operates under tight quality controls—an essential safeguard in aviation.
The Role of Induction Heating
In recent years, induction heating has emerged as a preferred method to heat-treat aerospace fasteners. Unlike large furnaces that heat entire batches slowly, induction heating uses electromagnetic fields to deliver focused energy directly into the metal. This approach offers several distinct advantages.
First, it provides precise and localized heating. The controlled electromagnetic field targets the exact section of the fastener that needs to be heated, avoiding unintended hot or cold spots. This is critical for achieving uniform microstructures, since uneven heating can lead to micro-cracks or other structural weaknesses.
Second, induction heating is fast and energy-efficient. Traditional furnaces may take hours to reach target temperatures and cool down, but induction systems can heat parts almost instantly, reducing oxidation and scaling in the process.
Lastly, induction technology is highly repeatable. Modern systems incorporate closed-loop controls that monitor temperature in real time, adjusting power output or ramp rates to maintain consistent conditions. These data-driven processes translate into better traceability—exactly what NADCAP auditors want to see.
What You Need to Know
Meeting NADCAP Requirements
Temperature Uniformity and Ramp Rates
NADCAP requires heat-treatment environments to maintain strict temperature tolerances. For fastener manufacturers, demonstrating uniform heating and controlled ramp rates is essential. Induction heating excels here by using tailored coil designs and responsive electronic controls, ensuring each batch of fasteners is exposed to the right temperatures for the appropriate dwell times.
Calibration and Maintenance of Equipment
A system that once performed flawlessly can drift out of calibration as components wear or sensors become offset. NADCAP places a high premium on detailed documentation, so each power supply, sensor, and coil must be regularly inspected and logged. From maintenance checks to software updates, every action should be recorded for easy audit retrieval.
Traceability and Process Control
If a defect appears in a finished batch, investigators need to review the “heat history”—the exact temperature profile and dwell time each part experienced. Modern induction systems simplify this requirement by automatically recording process parameters, creating a clear, digital audit trail that supports NADCAP’s meticulous documentation standards.
AMS Considerations
Alloy-Specific Requirements
While NADCAP scrutinizes how you follow heat-treatment protocols, AMS (Aerospace Material Specifications) focuses on the final properties of each alloy. Fasteners may be made from steel, titanium, Inconel, or other high-performance metals—each requiring a unique combination of coil design, frequency, dwell time, and cooling methods.
Avoiding Overheating and Underheating
AMS also defines hardness ranges and other mechanical properties. Overheating can lead to grain growth or embrittlement, while underheating may result in insufficient strength. Induction heating’s precise temperature control reduces the risk of either extreme, ensuring compliance with the strict quality targets set by AMS.
Quality Control and Testing Protocols
A robust testing strategy is critical for closing the loop on NADCAP and AMS compliance:
- Non-Destructive Testing (NDT): Methods like eddy current or ultrasonic analysis spot cracks and material inconsistencies without destroying parts—especially important for large-volume production runs.
- Destructive Testing: Randomly selected fasteners undergo hardness checks, tensile pulls, or microstructure analysis. These data points confirm that the induction heat-treatment process meets AMS standards for mechanical performance.
The combination of digital process records, NDT data, and destructive test results proves that each step has been properly executed and documented—a key factor in passing NADCAP audits.
Future Trends in Induction Heat Treatment
Automation and Smart Systems
More aerospace facilities are moving toward robotic handling and IoT-enabled sensors. This not only reduces human error but also allows predictive algorithms to flag potential issues—like coil wear or temperature drift—before they affect product quality. Digital logs can then be shared seamlessly with auditors.
Sustainability
With the aerospace industry placing increased emphasis on energy savings and carbon footprint reduction, induction heating stands out. Quick startup times and localized energy transfer mean less wasted energy and fewer emissions, supporting broader environmental goals.
Conclusion
In the end, induction heating offers aerospace fastener manufacturers a robust, versatile method to satisfy both NADCAP (process adherence) and AMS (final alloy properties) standards.
Its precision, speed, and comprehensive data tracking align perfectly with an industry where safety, reliability, and efficiency are paramount.
As aerospace continues to evolve—embracing new alloys, tighter tolerances, and greener production practices—induction heating is poised to remain integral to ensuring the highest quality standards in flight-critical components.
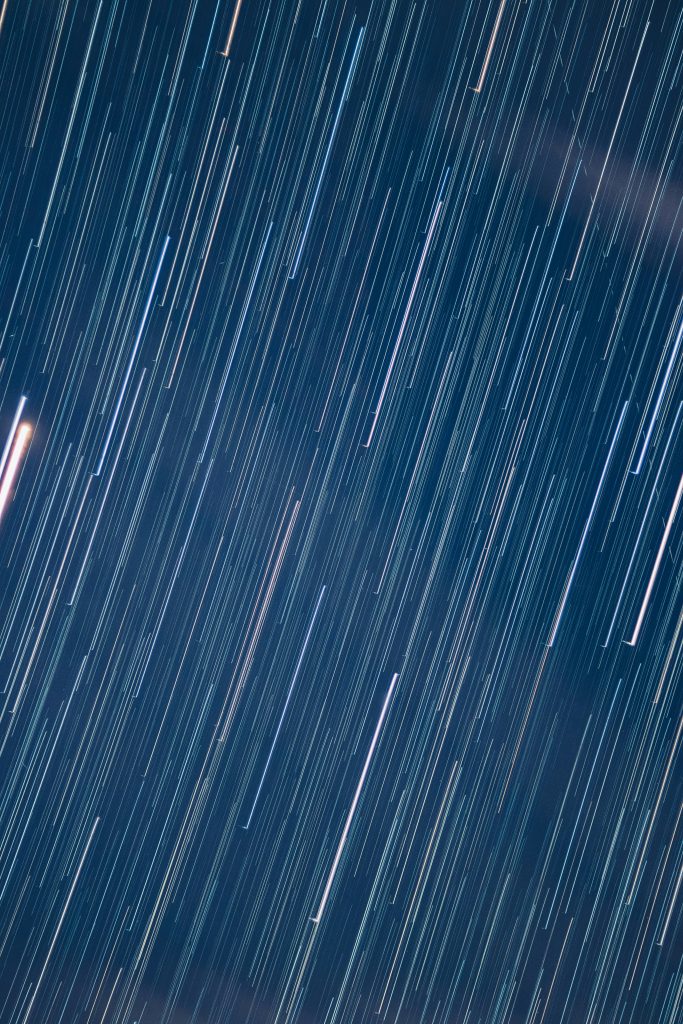
NADCAP & AMS at a Glance
NADCAP (National Aerospace and Defense Contractors Accreditation Program)
- Focus: Ensures special processes—like heat treatment—are performed consistently and meet aerospace quality standards.
- Key Points:
- Calibration & Maintenance: Equipment, including induction coils and power supplies, must be regularly checked and documented for accuracy.
- Consistency & Uniformity: Auditors look for strict temperature uniformity and repeatable parameters.
- Process Control & Documentation: Requires thorough record-keeping of temperatures, equipment maintenance, and operator qualifications.
AMS (Aerospace Material Specifications)
- Focus: Defines specific material properties and acceptable manufacturing processes (temperatures, soak times, cooling methods).
- Key Points:
- Alloy-Specific Guidelines: Covers steels, titanium, Inconel, and more, detailing how each should be heat-treated.
- Mechanical Properties: Lists acceptable hardness, tensile strength, and microstructure requirements.
- Testing Requirements: Calls for destructive (hardness, tensile) or non-destructive (eddy current, ultrasonic) methods to confirm specs.
Bringing Them Together
Result: A comprehensive framework that assures quality, safety, and consistency—from the heat-treat process to the finished aerospace-grade fastener.
NADCAP: Verifies how induction heating is conducted (process control, documentation).
AMS: Outlines what the final properties of each fastener should be.