Resistance Welding Equipment
Home » Resistance Welding
- Resistance Welding Equipment
Spot Welders, Seam Welders, and More
Resistance welding is a process that uses electric current to join two or more metal parts together. Heating Technology Source offers a range of resistance welding machines, including spot welders, seam welders, and projection welders. These machines are used in various industries, such as automotive, construction, and electronics.
Download CEA RESTECH’s Resistance Welding guide to learn more about this equipment.
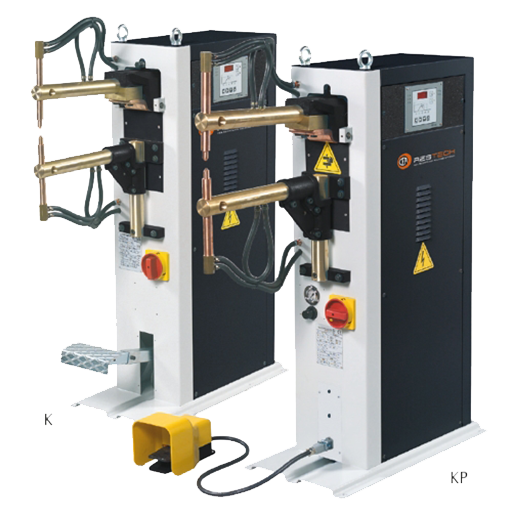
- K and KP Series
- Z and ZP series
- PPS Series
- BSW Series
- PPN Series
- MF 100 – MF 160 – MF 200
- MF 1040 – MF 1041 – MF 5020
K – KP
RESISTANCE WELDING
FEATURE
- Excellent welding on all weldable metals
- Electronic adjustment of the welding current and time
- Synchronous ignition SCR group with phase shift welding current adjustment to eliminate initial transient
- Reduced consumption
- Water cooled arms
- Water cooled copper electrodeholders with adjustable height
- Self-lubricated pneumatic components to eliminate oil deposits and to safeguard the environment from contaminants (ZP)
- High versatility thanks to all different possible work configurations
- Lower arm with adjustable height which can be rotated for use with a longer electrodeholder (Optional K/KP)
Z – ZP
RESISTANCE WELDINGZ and ZP series resistance spot welders, versatile, robust and easy-to-use, ensure best welding results on any weldable metal and are the most ideal solution for all spot welding applications. Z models are supplied mechanically operated pedal, whilest ZP are pneumatically operated by electric pedal FEATURES
- Excellent welding on all weldable metals
- Electronic adjustment of the welding current and time
- Synchronous ignition SCR group with phase shift welding current adjustment to eliminate initial transient
- Reduced consumption
- Water cooled arms
- Water cooled copper electrodeholders with adjustable height
- Self-lubricated pneumatic components to eliminate oil deposits and to safeguard the environment from contaminants (ZP)
- High versatility thanks to all different possible work configurations
PPS
VERTICAL STROKE SPOT WELDERS
FEATURES
- Excellent welding on all weldable metals
- Synchronous ignition SCR group with phase shift welding current adjustment to eliminate initial transient
- Thermostatic protection on the SCR group
- High welding currents with low consumption
- Self-lubricated pneumatic components to eliminate oil deposits and to safeguard the environment from contaminants
- Water cooled secondary circuit, i.e. electrodes, electrodeholders and transformer, to avoid overheating
- Water cooled copper electrodeholders with adjustable height
- Electrode force adjustable by pressure reducer group equipped with a manometer and filter for automatic air impurity expulsion
- Upper electrode movement by self-lubricated double effect pneumatic cylinder fitted with speed regulator, end stroke shock-absorber and silencer for compressed air discharge
- Manual valve for upper head descent without pressure for cleaning, centering and ordinary maintenance of the electrodes
- Solenoid valve to control welding cylinder
- Cycle stop emergency button
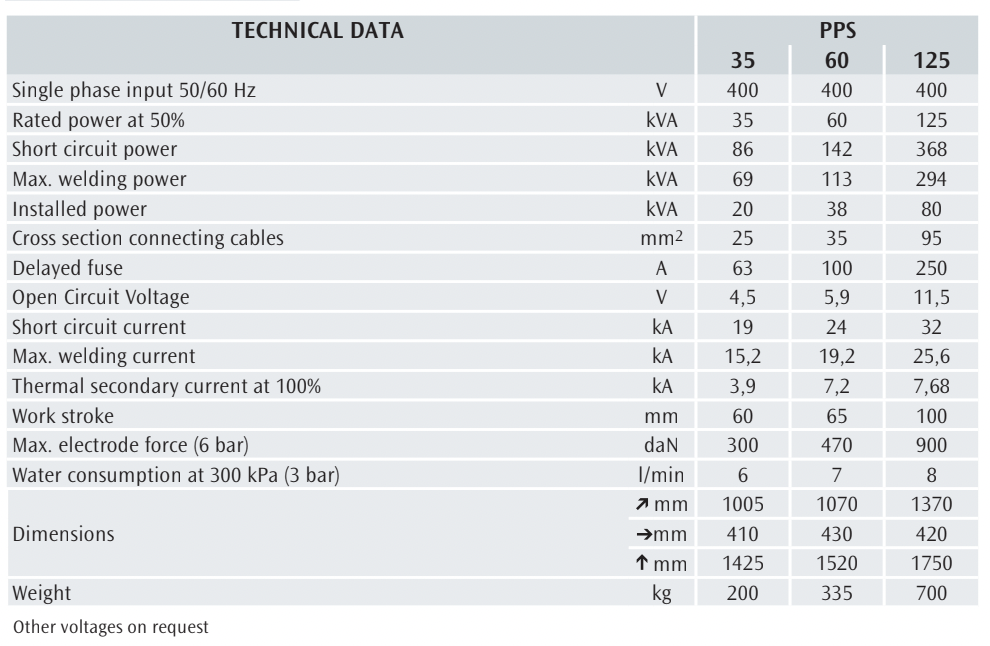
BSW
VERTICAL STROKE SPOT AND PROJECTION BENCH WELDERS / DIRECT CURRENT THREE-PHASE RESISTANCE SPOT/PROJECTION WELDERS
FEATURES
- Upper head low friction driving system for very precise and quality
welding - Secondary circuit low impedance to grant high welding currents with
low consumption - BSW 50 and 100, with a platens adjustable in height and fitted with
T-slots, enable the quick assembly of barholders, electrodeholders and
any dedicated tooling for a specific application - Safety cycle start by means of concomitant side buttons or, as
alternative only if the operator can work in safe conditions, by electric
pedal. Either option can be chosen by a selector with removable key - Cycle stop emergency button
PPN
RESISTANCE WELDING
PPN 63 fully satisfy a wide range of the industrial applications are equipped with microprocessor control, safety concomitant side buttons, electric pedal and solenoid valve, upon request it can be fitted with special controls to suit any special configurations.
PPN 83, 103, 153 and 253, all supplied with lower platen adjustable in height and fitted with T-slots, enable the quick assembly of bar holders, of electrode holders or any dedicated tooling for a specific application.
Platens gap is easily and quickly adjustable without any intervention on the secondary circuit (patent pending).
- Manual valve for upper head descent without pressure for cleaning, centering and ordinary maintenance of the electrodes.
- Upper head linear bearing driving system for precision welding (except PPN 83)
- Manual valve for upper head descent without pressure for cleaning, centering and ordinary maintenance of the electrodes.
- Upper head linear bearing driving system for precision welding (except PPN 83)