Applications
Home » Applications
- Applications
Induction Heating Applications
Induction heating is a method of heating an electrically conductive material, typically metal, by using electromagnetic induction. It relies on the principle of inducing eddy currents within the material to generate heat. Those currents encounter resistance within the material, and this resistance leads to the conversion of electrical energy into heat. As a result, the material heats up rapidly and uniformly due to the internal heating effect of the eddy currents. The heating is highly localized, focusing on the part of the material within the coil or the region influenced by the magnetic field.
Induction heating is done without physical contact on any ferrous or non-ferrous metals. The depth of penetration of the magnetic field is determined by the frequency used.
Induction heating is favored for its efficiency, speed, and precise control over temperature. It is widely used in various industrial applications, including metal hardening, annealing, forging, brazing, and even in consumer appliances like induction cooktops, where it provides rapid and energy-efficient cooking by directly heating the cookware.
There are many of these applications that induction heating can benefit in your facility. Here are just a few:
- Heat Treating (Hardening/Annealing/Tempering)
- Hot Heading/Wire Heating
- Crystal Growing
- Brazing/Soldering
- Forging/Hot Forming
- Shrink Fitting
- Melting
- Preheat to Welding
- Bonding/Curing
- Patch Coating
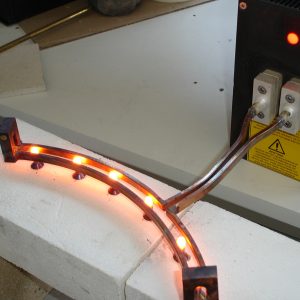
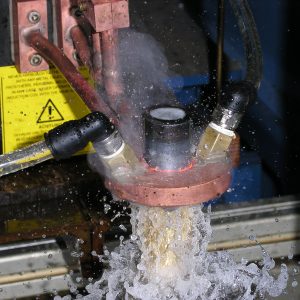
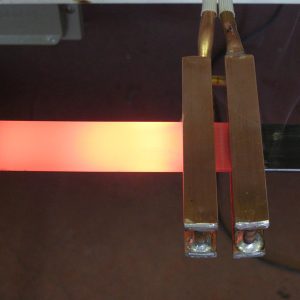
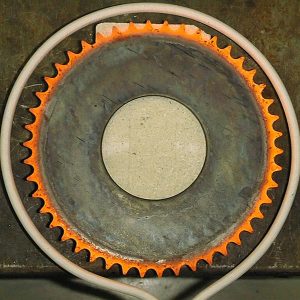
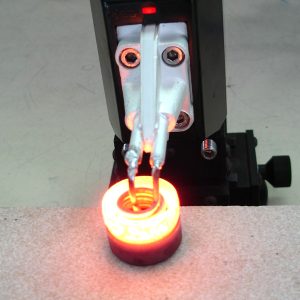
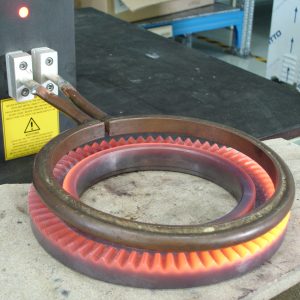
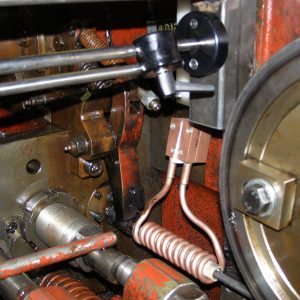
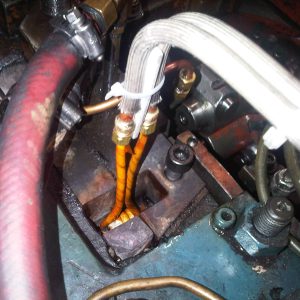
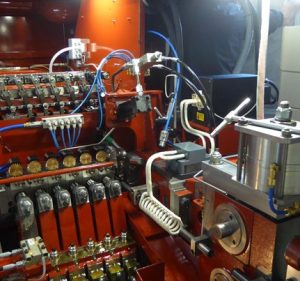
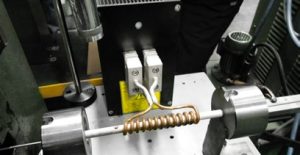
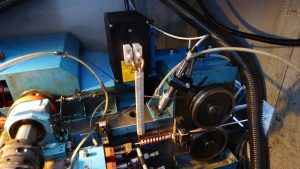
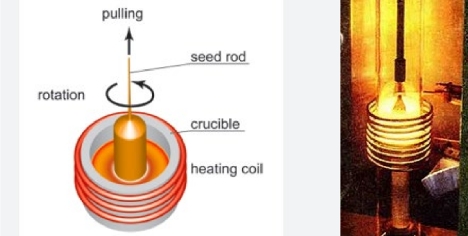
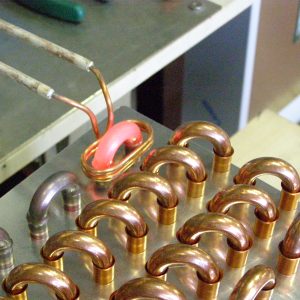
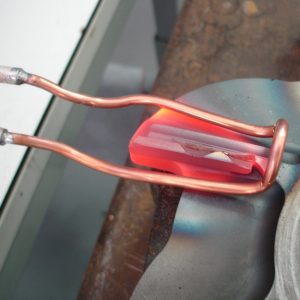
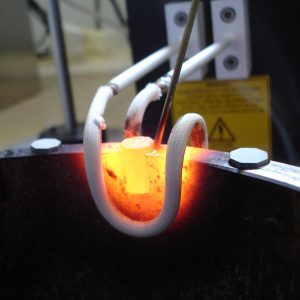
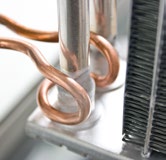
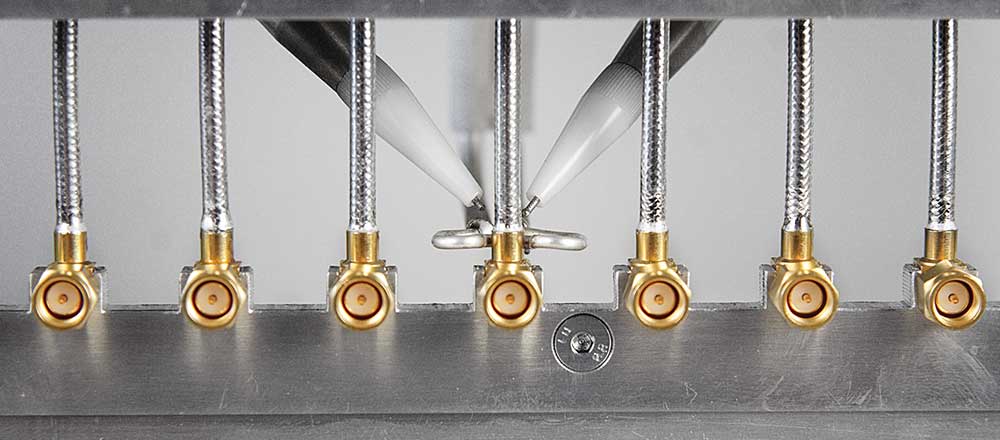
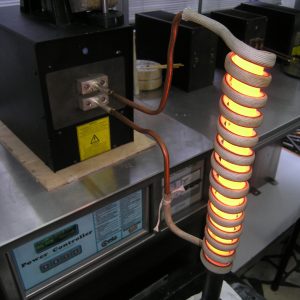
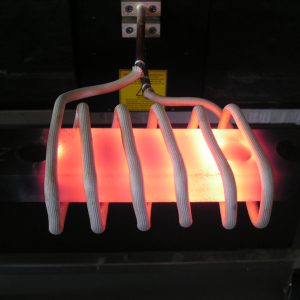
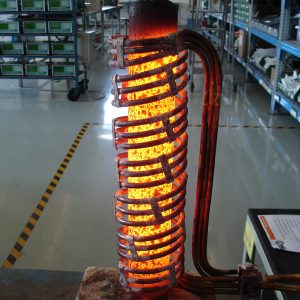
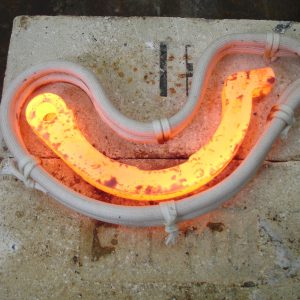
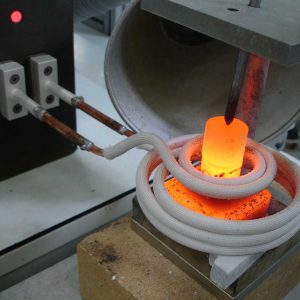
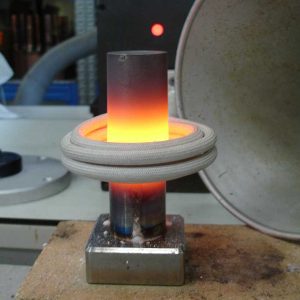
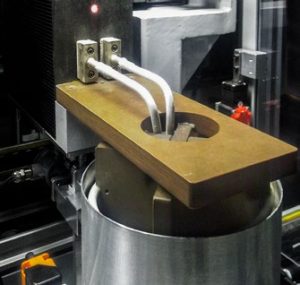

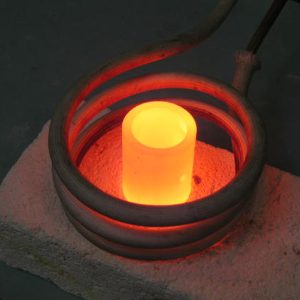
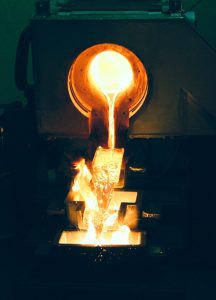
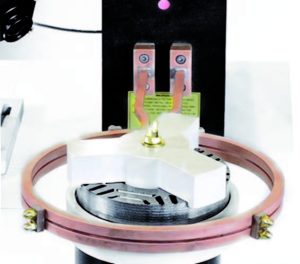
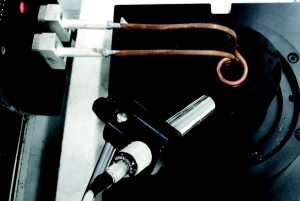
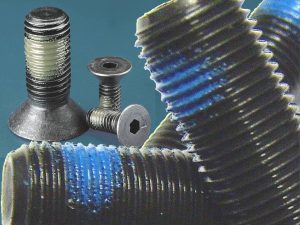
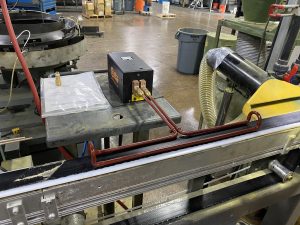
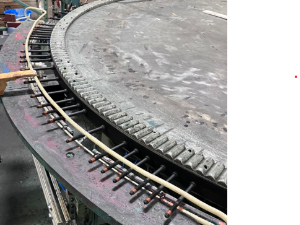